NEWS to EWES: An Example Budget Estimate for a 100-Ewe Flock
- Dr. Donald G. Ely
- May 10, 2024
- 11 min read

By Donald G. Ely, University of Kentucky
Introduction
The sheep numbers in the eastern United States have been growing mainly because, with correct management, sheep raising can be a profitable enterprise. Compared with other livestock, sheep are easy to handle and do not require elaborate and expensive equipment and facilities to be a productive unit. They are one of the most environmentally friendly livestock and can provide income from meat, wool, and/or milk. Sheep offer a significant advantage over other enterprises for beginning or part-time farmers because they require a relatively small investment per dollar of income. A few years ago, Iowa State University (Duffy, M. and J. Calvert. 2010. Enterprise Budget: Sheep, Beginning Farmer Center, 4 pages) assessed some variables, on a low, medium, or high scale, that are a part of a successful sheep enterprise. Variables and assessments are listed below:
1) Capital needed for startup Low
2) Managerial input needed Medium
3) Labor input required Medium
4) Years needed to develop production expertise Low
5) Years needed to develop marketing expertise Medium
6) Years to financial break-even point Low
7) Return on investment (%) High
It seems that potential sheep producers should develop an economic budget so, in turn, they can eventually assess the success of their operation. In other words, they need to assess whether they are making a profit or not. Seasoned producers likely operate within an established budget and have completed their assessment of the variables listed above. Still, they need to continually “fine-tune” their budget to increase their profit potential. Therefore, the purpose of this article is to provide an “example” budget for a 100-ewe flock that produces slaughter lambs from a January/February lambing.
Assumptions
The example budget in this article is based on the following assumptions:
1) Number of ewes = 100
2) Percent lamb crop raised = 160
3) Adult death loss = 5%
4) Ewe replacement rate = 20%
5) Number of rams = 4
6) Ram replacement rate = 20%
Although the average flock size in Kentucky is only about 19 ewes, 100 head are needed for a sheep enterprise to warrant efficient labor usage and make efficient use of feed and facility resources. In addition, 100 ewes are about the minimum number necessary to exert significant selection pressure if producers are raising their own replacement ewes.
For 100 ewes, it is assumed that 160 lambs will be raised to market weight. The 160% lamb crop raised is typical for flocks that have average to high levels of reproduction management expertise. Average prolificacy values for some pure breeds are published. Some are higher than 160%; others are lower. Prolificacy of non-purebred ewes varies with breeds making up the crossbreds. Therefore, a 160% lamb crop is assumed for this budget because other published budgets used this value and it is probably representative of the percent lamb crop raised for all breeds and crossbreds produced in the U.S.
On average, and even with top management, about 5% of adult sheep die during the year due to age, injury, predation, metabolic disorders, etc. In the budget, the 5 of 100 ewes that expire have to be counted in the 100 ewe flock. They incur expenses, but may or may not provide any return. It is assumed that another 15 ewes will be culled after lambs are weaned. Reasons for culling include age, structure and/or udder problems, injury, poor performance, or poor disposition (mothering and milking characteristics).
When lambs reach market weights, 20 ewe lambs are selected to replace culled ewes. These ewe lambs are likely born and raised as twins or triplets raised as twins and are in the top two-thirds of all lambs for daily gain from birth to weaning. As a result, they are some of the heaviest lambs at weaning and their post-weaning gains are among the highest in the flock. They are the most structurally correct of all the ewe lambs available for selection.
Four rams can be mated to approximately 25 ewes each for a breeding season from August 15 to October 1. Although mature rams (over 2 years of age) can service up to 50 ewes in a 6-week breeding season, ram lambs can service only 15 to 25 and yearlings 25 to 35 ewes in the same length of breeding season. Mating each ram to only 25 ewes adds genetic variation to the subsequent lamb crop which, in turn, allows selection of replacement ewe lambs to be mated to rams of different genetic make-ups. Finally, rams can become injured, crippled, and/or sterile before or during a breeding season. Then, the number of ewes per breeding group (ram) has to be increased to make sure all ewes are serviced.
A new ram should be purchased every year as one is culled. An average ram can normally remain productive for five breeding seasons (years). Thereafter, he can become sterile, injured, unable to mount ewes in the mating process, or his body condition may decrease to the point that he is unable to settle ewes satisfactorily. Also, some of the ewe flock will likely carry each ram’s genetics. When this becomes too extensive for individual rams, they need to be culled to prevent excess inbreeding.
The Budget
Table 1 identifies sources and amounts of income from a 100-ewe flock. Tables 2, 3, and 5 supply hay and grain, pasture, and other costs, respectively, required for 100 ewes to raise 160 lambs to 100 to 110 lb each year. Table 6 is a summary table of tables 1, 2, 3, and 5. Table 4 is the ingredient composition of a complete feed mix with a concentrate pellet. When studying these tables, remember every producer’s situation is different with regard to income, costs of production, and management. Therefore, the purpose of this example budget is to provide a guide that individual producers can use to develop their own budgets.
Income
Income shown in Table 1 includes proceeds from the sale of lambs, cull ewes and rams, and wool.

Lamb prices vary from year to year, season of the year, quality and sex of lambs, and marketing methods. Typically, prices per pound for 100 to 120-lb lambs are highest in the spring and lowest in the summer. Normally, the higher the quality, within sex (rams, wethers, ewes) and weight groups (60 to 80, 80 to 100, 100 to 120, 120 to 140 lb), the higher the live lamb prices per pound. Lighter weight lambs usually bring more per pound than heavy weights, but less per head. Prices received for 110-lb lambs can also vary by marketing method – stockyards, direct marketing to slaughter plants, individual (entrepreneur) sales, etc.
Prices for cull ewes and rams also vary within and among years. Extremely thin or fat sheep are usually discounted at the market. All cull ewes and rams sold through a stockyards must go to slaughter. Never buy breeding stock from the stockyards. If “culls” are still healthy and sound, they might be productive for other producers for a year or two. These sales have to be made on an individual producer basis, thus, prices may be higher or lower than shown in Table 1.
Wool prices vary by year, types/grades of wool, and marketing methods. Year to year variation is primarily a result of the world wool market that is dominated by Australia. Although individual producers are at the mercy of this world market, they can have an effect on the price they receive for their wool on the commodity market. Totally white fleeces (no dark fibers) with the smallest fiber diameter, the most crimps, the cleanest, and the longest staple length will sell for highest prices on the commodity market every year. The value per pound for the wool in Table 1 is assumed to be white wool that is shorn one time per year, is medium quality (1/2 blood, 3/8 blood, 1/4 blood, or low 1/4 blood), is typical of commercial sheep in the eastern half the U.S., and is normally produced by flocks where the primary income is derived from the sale of lambs rather than wool.
Expenses
Although producers may believe the only way to make more money raising sheep is to increase total income, a more realistic way to increase net income is to reduce expenses and/or increase productivity. Feed costs are usually the largest expense for any livestock enterprise. These costs are usually for hay, grain, minerals, and pasture for ewes, rams, replacements, and lambs. Example hay and grain cost estimates are presented in Table 2. Pasture cost estimates are shown in Table 3.
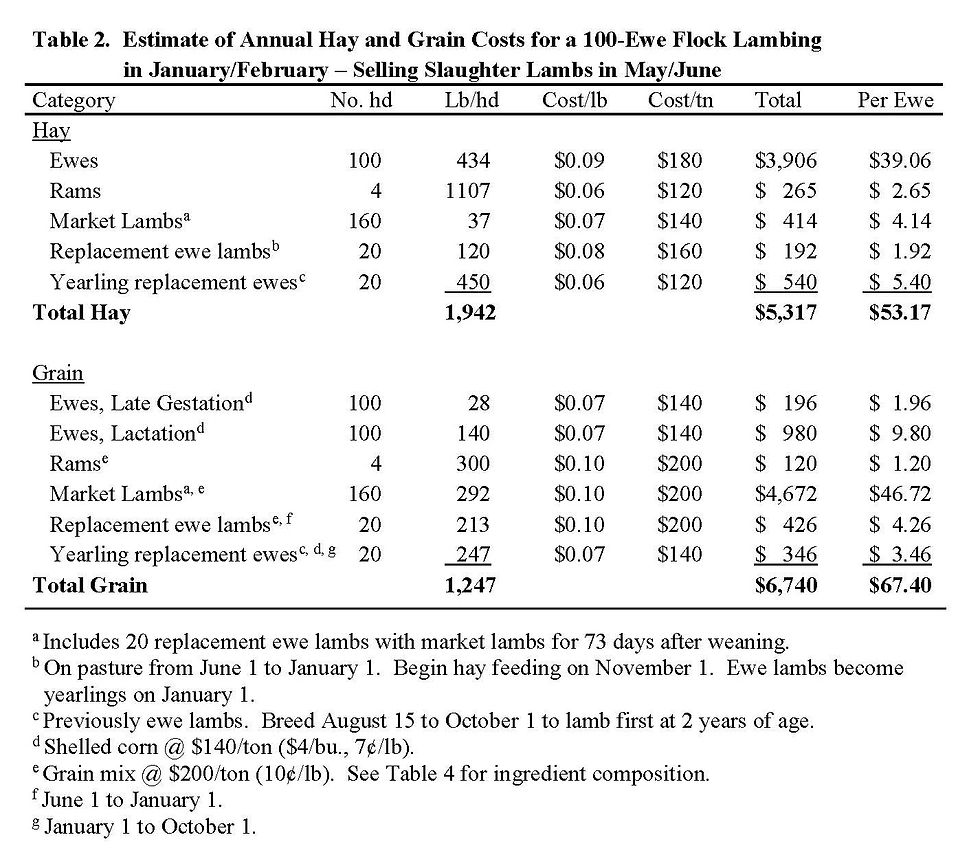

All classes of animals in a January/February lambing sheep enterprise consume some hay, as illustrated in Table 2. Amounts and types of hay consumed varies with the productive function by class of animal (Example: mature ewes vs. replacement ewe lambs). Total cost of hay feeding then is a function of the cost per ton.
It is assumed that ewes consume 84 lb/hd of alfalfa hay (mid-bloom) for 28 days of late gestation (LG) equaling 3 lb/hd/d. They are fed 350 lb/hd of the same quality hay during lactation. In this example, rams consume the most total hay, but it is lower quality than that fed to ewes. Rams remain in confinement for most of the year to prevent injury, sterility, or other unforeseen occurrences and have to be fed some low-quality grass hay to maintain mature weights. Whether replacement ewe lambs, that become yearlings on January 1, need the quality and quantity of hay shown in Table 2 may depend on the weather, stockpiled forage availability, and/or alternative forage availability. However, after January 1, they will, for sure, need low quality hay plus daily concentrate supplementation until spring pasture becomes available.
The only times that ewes receive grain supplementation in this example is during LG and lactation (Lact). The combination of alfalfa hay and shelled corn fed during these production phases will result in balanced rations if fed in correct amounts. Rams consume a grain mix (1.0 lb/hd/d) to supplement low quality hay consumption, while in confinement, to maintain body weights. Ingredient composition of the grain mix is shown in Table 4. Market lambs are self-fed this grain mix from creep feeding to market (average intake = 4.0 lb/hd/d). Replacement ewe lambs are also self-fed this grain mix for 73 days after weaning. Thereafter, they are supplemented with 1.0 lb grain mix/hd/d from June 1 to January 1. Grain supplementation is switched to shelled corn on January 1 and will continue to be fed at 1.0 lb/hd/d until October 1 (274 days; after first breeding).
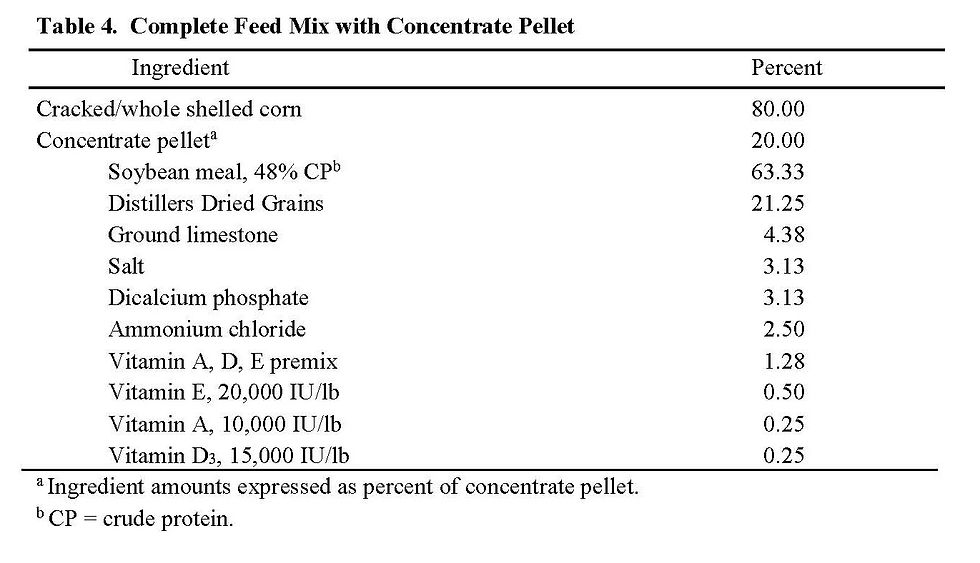
Total grain cost per ewe is greater than total hay cost ($67.40 vs. $53.17). Most of the grain cost per ewe was expended on the market lambs ($46.72), whereas the hay cost was expended on ewes ($39.06). Table 3 shows a total pasture cost of $16.91 per ewe. This table illustrates that ewes, rams, replacement ewe lambs, and yearling replacement ewes are on pasture 267, 45, 213, and 274 days per year, respectively. Market lambs are raised in total confinement from birth to market in this example.
Other costs
Estimates of other costs are summarized in Table 5. Vet/medicine costs include deworming and vaccinations. In this example, ewes are dewormed twice, rams once, and replacements twice per year. Market lambs are raised in confinement, so do not need to be dewormed. Lambs are vaccinated at 5, 8, and 11 weeks of age with CD/T (Enterotoxemia Types C and D as well as Tetanus). Ewes are boostered annually. The $8.30 cost per ewe includes medicines for pneumonia, scours, mastitis, and any other diseases/disorders that may arise during the annual production year.

If wool sheep are raised and shearers are hired, costs probably reach at least $4 to $5/ewe for once a year shearing. This budget item in Table 5 will obviously be zero if producers do their own shearing or if they raise hair sheep.
This example budget assumes one replacement ram is purchased each year to replace a mature ram that has been used for 4 to 5 years and serviced 100 ewes during his productive life. Continually introducing new genetics will reduce inbreeding. Costs of rams vary by age, breed, and production records. Although the $700 cost of replacement rams in this example may seem excessive, remember that 80 to 90% of the genetic improvement in a flock comes from the ram. When the genetics of rams are spread across the lambs from 100 ewes mated, the $7.00/ewe/yr does not seem too expensive.
Successful lambing in January/February requires some kind of protection from the weather. This means ewes will lamb on some kind of bedding in a confined area (barn). Bedding can come from wheat or rye straw, hay, wood shavings, and/or newspaper. Variation in types of bedding means variation in costs. The value for bedding in Table 5 was calculated from estimates made by the University of Maryland, Virginia Tech, and personal experience at the University of Kentucky. Similarly, costs of hauling animals to market were estimated by these three universities.
Mature sheep typically will consume about one pound of salt/mineral per head per month (12 lb/yr). The amount of salt in the mineral mix regulates the total consumption rate. Many complete mineral mixes, sold commercially, are highly palatable. Consequently, sheep consume more than needed if the mix is not diluted with 50% white salt. The consumption rate and cost of the mineral in Table 5 are based on diluting the complete mix with 50% white salt. This decrease in intake need not be alarming because, theoretically, normal daily intakes of balanced rations of roughages and concentrates will meet the mineral (except salt) needs of the animal. Ad libitum supplementation, in reality, may only be a safety factor.
Checkoff costs may not be charged in all states. If charged, they can vary from state to state. The cost in Kentucky is $0.50/100 lb live animal marketed (Table 5).
The January/February lambing system will require the barn bedding containing, manure, urine, etc. to be removed at least once a year. If the bedding is on dirt, after removal, apply Class I2 sand to the surface for drying. Building/fence repairs will vary from farm to farm, age of buildings/fences, and types of buildings/fences. The $3.00 expenditure per ewe per year for these repairs is the same as used in budgets published by Iowa State University (Mike Duffy, Jodi Calvert, and Dan Morrical. 2010. Enterprise Budget : Sheep, Beginning Farmer Center – BFC 18), University of Missouri (Ron Plain, Extension Economist: Ewe Flock, Projected Budget for Lambs Sold in 2011), and Virginia Tech (Virginia Cooperative Extension Farm Business Management Staff. 2011. Sheep : Spring Lambing; Raise Replacements, Publication 446-048.). Purchase, maintenance, feed, and health care costs contribute to the cost if the farm uses a guard dog for sheep protection. The interest cost ($4.80 per ewe per year) is on operating money. In other words, if you are not a sheep producer and have invested equivalent money, how much can you make? The $16,000 borrowed is charged for 6 months at 6% interest.
Table 6 summarizes the income vs. expenses and the return to capital and labor. In this example budget, 91% of the annual income is from the sale of 100 to 120-lb (Av. 110-lb) slaughter lambs at 4 to 5 months of age (Table 1). Of the total expenses (Table 6), 73% is spent on feed (hay, grain, pasture) consumed by ewes, rams, lambs, and replacements (Tables 2 and 3). Hay cost makes up 56% of the total feed costs. Surprisingly, lamb feed amounted to only 37% of the total annual feed costs.
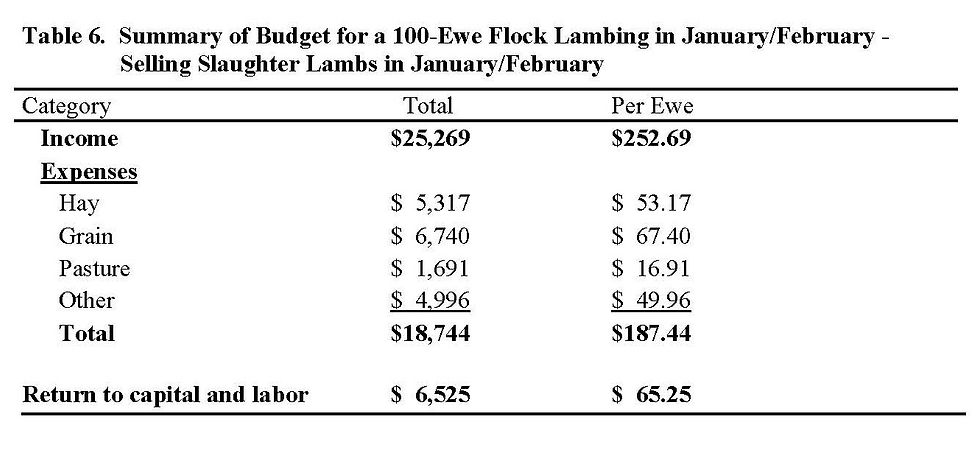
Implications
Finding two sheep production operations that are the same and have a stable expense/income on a daily, monthly, or yearly basis is an impossible task. Therefore, developing a budget that will fit every situation is impossible. Consequently, a budget, like the one presented in this paper, can be used only as a guide. On the other hand, today’s technology allows keeping immaculate income and expense records as never before. Incorporating these into a budget format will show where income is derived and where dollars are expended. Maintenance of a daily diary for the production year, that begins on the first day of the breeding season, will explain why money movement was income or expense on a specific day. Then, analysis of the individually constructed budget will show where management efficiency can improve from one year to the next.
Dr. Donald G. Ely, Professor in the Department of Animal and Food Sciences at the University of Kentucky
Comments